Training and retaining labor on dairy farms
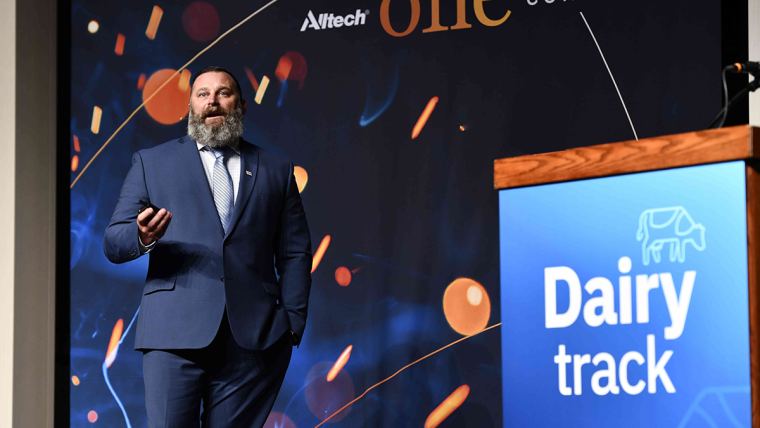
Prior to joining Alltech, Dr. Luke Miller practiced as a large animal veterinarian and served as the general manager of a 6,000-head, multi-site dairy in central California.
How can dairy producers overcome labor shortages? Dr. Luke Miller, dairy technical support specialist at Alltech, joins the Ag Future podcast to discuss how dairy farms can attract, train and retain labor, as well as his thoughts on the future of hiring as dairies adopt more automation in their operations.
The following is an edited transcript of the Ag Future podcast episode with Dr. Luke Miller hosted by Tom Martin. Click below to hear the full audio or listen to the episode on Apple Podcasts, Spotify or Google Podcasts.
Tom: Welcome to Ag Future, presented by Alltech. Join us from the 2022 Alltech ONE Conference as we explore opportunities within agri-food, business and beyond.
I'm Tom Martin for the Alltech Ag Future podcast series. We hear about this from every segment of the economy: Labor — most acute in industries that call on workers to perform especially hard work — is a big concern these days. That definitely goes for the dairy industry. How do we properly manage and train employees so our farms can be successful for years to come?
That question brings Dr. Luke Miller to Ag Future. A veterinarian, Dr. Miller is a dairy technical support specialist at Alltech with expertise in every level of the dairy operation. Before joining Alltech, Miller was the general manager of a 6,000-head multisite dairy in central California, managing operations and a team of 45 employees and designing and building a state-of-the-art, 80-stall rotary milking barn. He's worked with local and national government agencies on grants and permitting. For eight years, he served as a large-animal veterinarian and eventually became the owner of a practice that addresses all facets of large-animal medicine. Dr. Miller also aided in the design and implementation of dairy protocols and standard operating procedures. Thanks for joining us, Dr. Miller.
Luke: Good morning, and thank you very much for having me on. I really appreciate the invitation.
Tom: As I said, labor has been and is a major concern for the dairy industry. The prospects of that changing anytime soon are pretty bleak.
Luke: Slim to none.
Tom: How should we educate dairymen in the ag community about what the labor force really looks like now, and how we might go about retaining teammates that we want to keep?
Luke: The basics to begin with are to start understanding who we're trying to hire and understanding where they came from and their basic levels of both education and interest in the group, in the dairy. We know that many of our laborers are not loyal to a particular place or particular farm, so we try to invest in them as much as we can and get them to want to be with us, (since they) want to be wanted. That's kind of one of those deals. Everybody appreciates it when you're a good employee. How do we keep those people once they're good? Losing good employees is never, never a positive. We want to retain the good ones and sort the proverbial wheat from the chaff as much as we can when we're getting new employees running through the dairy on almost a daily to weekly basis.
Tom: Let's say you're somebody with an operation that's experiencing this and you want to do that — you want to figure out how to retain people. What are some ways to do that?
Luke: I think one of the basics is knowing and having an organizational chart. I preach this every place I go, that — understanding employees want to have a box. They know where the top is and know where the bottom is. They want to be put in that box, and they want to understand the basics of their job so that they can fulfill what you want them to do, and they feel like that’s gratifying to them. When they do a good job and you tell them they do a good job, that’s the thing. But I think a basic organizational chart is one of those keys that every dairy, no matter the size, should really have — especially small family farms that we deal with a lot, where an uncle or a dad or a mom or a cousin or a brother is on the dairy. Having them understand where they fit into the organization, how they move throughout the organization, up and down that organizational chart — it’s very important. So, I think that's one of those keys.
Tom: If we want to meet expectations, we need to know where they are.
Luke: Exactly. Right. That's the other part of it, is the job description. Very many of these dairies do not have any job descriptions for their employees. They are simply hired because you showed up that day. Yes, it's important to get the cows milked, to get the harvest in, to do many of the things that are daily emergencies on a dairy, but at the same time, we don't want to hire the wrong person to come in. Job descriptions and some early vetting of who we're actually bringing into the dairy is important.
Tom: Making that investment to attract, retain (and) educate employees can often be seen as a secondary priority in the grand scheme of things, but why is it so crucial that employers make it an operational priority?
Luke: I've had a couple of dairymen tell me, and I've kind of come to this one on my own, that if a car full of employees pulls up and we say — there's four or five people that are new to your dairy that pull up, and they say, "I want a job," very few of us dairymen at the time would say, "Nope, I don't have room for you." But in reality, at least 20%, at least one of those guys in that car, or girls in that car — (I) try not to do that anymore; we have a lot of new females in the dairy business — but someone in that car is going to hurt you, and it might be through OSHA. It might be through morale. You might turn around and six months later, your entire workforce has flipped over and it's a negative experience, and that is not what we want to do. We need to understand who we're bringing in.
So that first understanding of the damage that an employee can do to your operation may not be immediate. It may not be that day. You may not really see them. Obviously, the animal rights or animal welfare — somebody's trying to take advantage of your operation with film or with video, with audio recording — is also very damaging, and we want to limit that access as much as possible.
Tom: Does this involve some sort of an intake process where you can kind of tease out these issues?
Luke: An onboarding process is extremely important for dairies. I think that having the 10 questions, right? And they don't have to be my 10 or your 10 or anybody else's 10, but having the 10 for our dairy — you can sort a lot of things out if you just ask basics. The second step of that is (to) train the trainer. We have to have somebody on the dairy who knows how to train people, and we put them in charge of — not the hiring but the actual onboarding of the person when they start. We find a guy we like. We find someone we want to put on the dairy. We send them out with a trainer. You have an hour, two hours a day — whatever it takes to appreciate their skill level.
It's very obvious when somebody comes to us and says, "I can do this," and then you put them in that position and they can't do this. But you need to have trust in your trainer, a manager, even, or a lead or a foreman who can sort them out and say, “They have no idea what they're doing.” That puts flare one up in their file. They've already lied to us once. What else (in terms of) damage could they be doing?
Tom: Why is it important to make sure that employees are educated in stockmanship?
Luke: Stockmanship has come about in the last, probably, 20 years, and stockmanship has really been infinitely old(-fashioned) about how to handle an animal and how to deal with them. Thirty years ago, it wasn't a problem, because facilities were small, dairies were smaller. It was more mainly family-oriented — so a new stockmanship was going to happen because you were raised in it. But stockmanship is the basics of understanding animal husbandry. How do we move them? How do we speak to them? How do we work with them?
So many of our new employees now have absolutely no appreciation for stockmanship and have no appreciation for what it takes to just do the basics with an animal. That's one of those things we need to work with. Stockmanship training is very important. It's also not really that hard to teach. We go back to “train the trainer”. Follow somebody who knows how to do stockmanship and the basics: moving animals from one pen to another, giving medications to an animal. There are ways to do that where it's non-confrontational to the animal. It's easy. Everybody's calm. I go on dairies a lot where I know the stockmanship is good, and I can walk right in front of all the cows and nobody jumps, nobody moves, nobody runs. I go on to dairies where stockmanship is not good, and it's like a stampede every time somebody new comes into the pen. It's very obvious when stockmanship is a priority on dairies.
Tom: Have emerging technologies helped improve the dairy-farm work environment in some way?
Luke: That's a really plus/minus question. I think there are — technologies have made it really beneficial to know who you need to go work with as an employee with an animal. But at the same time, when you do a lot of emerging technologies, that tends to turn the animal back into a machine, and that's what we don't want to do. We do not want to have, “That's just a machine that makes milk.” Nope, that's a cow. She's an individual, and she might be individual 1,473, but she's still an individual, and appreciating her for what she does every day is different than making her a machine.
I do love emerging technologies. I think there are great things to be done with pedometers and necklaces and rumination collars and robots in the milking industry. But at the same time, you also have to have an appreciation that it's still a cow. It's still an individual, and we still do need stockmanship, and we still need to have that human-animal interaction.
Tom: Let's talk about that interaction between human and animal on a dairy operation and how critical that is for both the dairy and for peace of mind.
Luke: Yeah, it's something I just started learning more about. Having had one for a long time, you take it as just for granted that you know what a human-animal interaction is, and how it works is very similar with children. Their first interaction can often be, once they learn it, “It's bad” or “It's good,” and it takes a long time to train them out of (that thought process). So, if you think about doing something poor — you were shouting, you were loud, cows were scared — you have to have repeated interactions for that to go away, for them to be retrained.
(We need to be) teaching our employees who may have worked in a peach orchard or maybe have done seasonal labor and now they want to go into a full-time type of agricultural job that there's a difference between a peach tree and a cow. We need to have them understand that there's interaction. If you form that interaction good, the cows will appreciate you, they'll interact well with you, and they'll do what you want them to do. (This is) not highly researched, but it is out there, and it's getting better. Because of the human/animal welfare kind of exhibit, we see that actually trending in both ways, right? That's one of the big breakthroughs, is that, if you're good to cows, it can be enriching to your life. We've seen this in the service-animal industry for years. Everybody knows the commercial where the dog comes into the hospital and makes the kids feel better. It's the same kind of thing. Your job can be way more enriching if you like what you do, if you like the animals you work with. If you fight them all the time to get your work done, it becomes very unpleasant. That's why we lose a lot of our employees. They just don't understand that it can be enriching in reverse.
Tom: Does that become kind of a loop, a feedback loop? If you're uncomfortable with them, they sense that?
Luke: Yes. Oh, for sure. It's not just one worker. If you're doing the right thing during the day shift, the night-shift guy can be doing the wrong thing or the not-as-good thing, and the animals, when you come back, will feed on that as well. There's a positive and a negative feedback loop. The negative feedback loop is production. If we're rough, if we're tough, if we're too loud, if we cause some releases of pheromones that say, “We're scared,” we get decreased production. If we're good and we're happy and we move nicely, the cows just remain calm and everybody's good. That leads back to you as the employee, and you feel good about doing your job, and your boss doesn't yell at you. It is definitely a feedback loop, both positive and negative.
Tom: I'm imagining the (Gary) Larson cartoon here, and all the cattle are saying, "Oh, here comes a good one."
Luke: Oh, Gary was spot-on. I would say that if I was going to ever pick out a true advocate for agriculture and how it really is, Gary Larson is one of those guys. I think every vet's clinic in the universe has one of his calendars still on permanent repeat because so many of his things were so true. I don't know how he went from horses to cows to every facet of agriculture and nailed it.
Tom: It's fascinating. By the way, in the introduction, I mentioned that you had designed and built that state-of-the-art, 80-stall rotary milking barn. I wondered if that design has worked, in some way, to improve these interactions between human and animal.
Luke: It's a funny thing of rotary, and we see it with the robot barns that are coming now and the usage of more technology. But the robot (barns), they go to (them) on their own, and that was the design with the rotary, is we didn't want to bring them — we didn't want to force them into the milking barn. When you see cows ride a rotary, it's one of the funniest things. They walk on it of their own volition, and they go off of their own volition. It's the only time they move — aside from that one time at the end of their lifespan — for free. They don't have to walk, they're not to do anything, they get on, and they ride. You watch these cows come up. You never have to push them into the barn. That's a common thing with all new barns, is we need to get them into the milk barn to be milked. With rotaries, they line up and they get on and they ride. It's truly funny and exceptionally efficient when you don't have to have somebody do that. But it's one of those loops that we talked about. It's enriching for the guys, because I don't have to force them to get on. They want to get on. They get on that rotary and ride. Yes, that technology, that thought process, was in my brain when we decided to build that barn, was — what can I do to make it easier for them, also make it easier for my guys, and still get the efficiency and the production we need to be a viable dairy facility?
Tom: Sounds like another one for Larson.
Luke: Right. Yeah, you'll put the wings on when they fly around in a circle. It's right there.
Tom: Well, ultimately, the ultimate goal here is to produce. So why is a good human-animal bond good for production?
Luke: I don't know that it's any better for production when you have a good one. We do definitely know that it's bad when we have a bad one. This is one of those “do no harm, first” kind of deals, is — no matter what, we want to let them produce to their expectations. Given the genetics that we've bred into these cows over the last 30 years and the leaps and bounds that we've made there, we don't want to hinder that. To not hinder that, we want a good human-animal relationship. We don't have any research stating that if it's good, it's better (for production). We would have to go, probably, back to little, more companion animals to pull that out a little bit — dogs and cats and horses. In fact, that — we're going to see progress with that. We do know that any negative interaction does cause a negative consequence in production. Just be good. We're not expecting more. We just need “good”.
Tom: How about the human side of this equation? How does this bond affect human welfare and job performance and satisfaction, the things we were talking about earlier?
Luke: Yeah, I think retention is that key, right? If you work in a place where this is valued, you know that you're at a place that values you. This has been one of those recently formed ideas. Jorge Delgado was one of my compatriots here at Alltech. He brought this to me and said, “I think you need to talk about this.” We need to speak of it this way, is — we've educated and we've pushed dairymen and bosses across the country to teach employees to treat their animals like they want them treated, right? “Be good to my animals, because they're important to me, and I want you to be good to them.” I think we need to flip that a little bit — and it's worked in the cases that we've done it, which is “I don't want to treat the animals the way I want. I want to treat the employees the way that I want — to treat them well — and they will take care of my things.” It's the inverse, a little bit, of what we've been taught, and what we've worked on is getting job satisfaction, but we do that through treating the human well, and then the human will take care of our assets. And we've seen this work.
That is the opposite rule of, typically, “I want you to be good to my animals. I want you to take care of them. Don't hit them. Be nice to them and do these things. Don't break the tractor and go that way.” No, you know what? We're going to say, “I've fixed your house. I give you good bonuses. I'm treating you well. I say hi to you. I know your name. We interact with you. I treat you well. Because of the respect you will give me for treating you well, you will then treat my things well, which is important to me.”
To get back to your original one, retention is still the key. We want to keep the good ones there. We want to sort out the bad ones. But to do that, we need to get past a couple of weeks, we need to get past a couple of months, and show them that they're important to us — and that's really the key, is they are important to us. They are the basic cog in our industrial dairy. Without the people, we simply cannot do what we need to do. For too long, we have said, “Just bring another one in. Just get another person. Just revolve the door.” That's so expensive, and it's so damaging to morale. We need to be good with the ones we have. Train them. Train, train, train, train again, and then look at, “How do we make them happy so that they want to stay with us?”
Tom: Now, one thing I'm really curious about is — and we're talking about the environment now. (What I’m curious about is) whether or not music can play a role — certain genres of music, certain types of music — in calming cows as well as the people working.
Luke: I had this argument when I was running the dairy, and I walked into milk barns for 20 years that have had blaring music of various sorts. Obviously, in California, it's usually a little more Hispanic in flavor, but you can certainly go to the middle of Michigan, where I grew up, and hear (dairies) blaring classic rock. Cows are exceptionally adaptive to whatever we put in front of them. Once they're used to it, it becomes the norm. Yes, there is work out there that — saying calm, basic, smooth jazz or smooth classical music does relax the cows when they come in.
But if you've walked into most modern barns right now, I really don't want to hear anything. I don't want to hear humans yelling. I want to hear the machinery. The new machinery is quiet. The fans, you'll hear the buzz from the air, and you'll hear ambient noise in the background. But to me, that's how I know I'm on a place that's really well-run, is when I walk in and I don't have the blaring boombox in my ear when I walk in. Because it is about the cow, not about the human. I understand we need to be entertained.
And then, secondly, all I hear is cow, right? It's just breathing, chewing, hanging around, and a little bit of mooing. That's how I know cows are exceptionally calm, and that's one of those things — and calm before anything else. If they're calm with mariachi music, then they're calm with mariachi music. I don't have a problem with music, per se, in the milk barn. It's about the cows’ reaction to it. If everybody's tense and the workers are fast and they're moving and this and that, that's bad. We want everybody to be calm.
Tom: Well, to bring our conversation full-circle — this has been fascinating — would you come back around to the labor question and what it's like out there? Is it even possible, at this point, to think a decade ahead about what the labor market is going to look like? What do the next 10 years look like for dairy?
Luke: Yeah, that's a good question. I think the last 10 years have been really fun. I go to dairies now, and everybody, with the recent COVID pandemic, and everybody — not everybody — and people's lack of desire to work in the office and not come in, the dairymen are laughing, because they've been living this life for 30 years. If I don't want to come in there — so there’s the popular meme where the dude’s in the noose and looks over and goes, “Your first time?” And they're going to go, “No, it's not my first time at all.” They laugh and they think it's funny, because they've been dealing with this forever. This is nothing new to them. They've always been scrambling for workers and trying to get there.
I don't think that changes. I had a dairyman this week that we met with. We were on a tour this week with some visitors from out of the country that were, in fact, coming to the (Alltech ONE) Conference, that — he asked them, “Would you do it like this?” It was a new robot facility. “If you had a new place, would you build it like this?” He was pretty flat-out, and he said, “In California, no, I would build it just like this. If I was in another state, I'd probably build a rotary, because I think I could get people.”
It's not going to stop. Part of my talk that we go through is I want people to appreciate the fact that they're not a “milker”. They're a technician. We're asking them to do a very specific technical job, to remove a product from an animal and make it work for us for a profit. They're no longer “milkers”. We need to call them “teammates,” we need to call them “technicians,” and we need to value their position on the dairy. I think that we're never going to stop arguing about labor. It's an entry-level job. People are going to come to it, they're either going to like it or not like it, and they're going to leave.
The problem we're going to face is probably the rising wage issue of who we have to hire and how much we have to pay them to get (them) to do the job. California is going to go a lot more robots, because we are typically ahead of the curve when it comes to minimum wage, but in the next 10 years, I would expect to see a lot more automation. Unfortunately, that means that you’re going to have to pay your guys more, because they have to operate a really good computer to work with the automation you've put in front of them.
But I don't see it changing much, honestly. I think we'll see the same migrant labor force. People in the United States do not want to do this job. We've tried, right? We see it through the Midwest a little more. But on the West Coast, on the South coast, it's a migrant labor force. We're forced to deal with, “How do we train, educate and make them appreciate the job they have?” And we need to appreciate their labors. But, yeah, the answer is like, in this specific one question, it'll be the same problem (in) another 10 years. We'll just have more automation. We'll have more robots. We'll have removed, maybe, a few of those basic-level guys, but we'll have more mid-level guys. Maybe that's what we want, are some thinkers on the dairy.
Tom: Well, maybe we'll talk again in 10 years and see if it's the same or not, but it's certainly fascinating to think about. Dr. Luke Miller, dairy technical support specialist at Alltech. Thanks so much for joining us, Dr. Miller.
Luke: Thank you very much for having me.
Tom: For the Ag Future podcast, I'm Tom Martin. Thank you for joining us. Be sure to subscribe to Ag Future wherever you listen to podcasts.